A right amount of experience is needed to know the exact problem of existing Steel roof structure before adding a new Roof top unit with it as the work needs experienced methods to do.
Often contractors are asked to calculate a previous steel roof structure to establish if it can support new roof top units or not. Often tenants remodel commercial spaces for their needs and also sometime new air make-up units, exhaust fans and HVAC units need to add.
What is Roof Top Unit: A packaged rooftop unit or RTU is a kind of HVAC system that has all the components needed to supply conditioned air in one brief unit. Packaged rooftop units are naturally found in light and large commercial applications. They are very famous in the construction industry with retail and industrial properties.
The Roof-top Unit or Roof Top Air Handling Unit supplies Heating, Ventilation, and Air Conditioning (HVAC) to the space below. Air duct Smoke Detectors or Duct Detectors can be inside the Roof Top Unit or in the air ducts below it.
In this article we are going to show evaluations of two commercial spaces for new rooftop units; where one space was adding a commercial kitchen and needed new exhaust fans and air make-up unit while the other needed new cooling units to reverse all the extra heat that was coming.
New roof top units can be large and heavy and generally affect the existing roof structure; sp at first the existing roof structure is examined to know the size, space and span of the joists, location of bearing walls and girders and location of previous roof top units. Generally a typical commercial roof structure is constructed with steel bar joists which are mainly tagged by the manufacturer like Vulcraft who keep records of joists’ type to use in the projects. Next all the accurate measurements of the top and bottom flanges, the web members and the length of the joist has taken; besides all this contractors have to observe other parameters to make sure all new and previous load can be transferred to the supporting structure in the right way.
After that the ability of from the manufacturer is determined and/or is modeled as per its section properties which help the contractors to calculate the load carrying capacity of the steel joist. As previous joists don’t have a lot of extra load carrying capacity so they can be strengthened by welding steel rods and plates to the flanges. But it is always best to locate a new unit away from previous units and near the previous bearing wall or girder which will limit the amount of new load on the previous joints. So basically it is mandatory to examine a previous structure to know its strength and capacity and qualifying it accordingly the new one as it creates a good understanding of structural design as well as a wealth of knowledge of building construction.
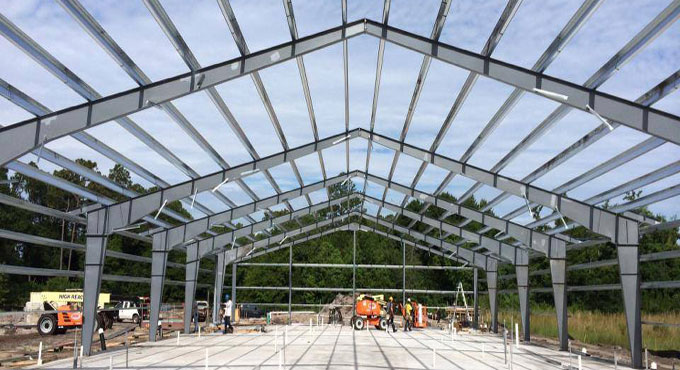
Read more
~~~~~~~~~~~~~~~~~~~~~~~~
Published By
Rajib Dey
www.constructioncost.co
~~~~~~~~~~~~~~~~~~~~~~~~
Often contractors are asked to calculate a previous steel roof structure to establish if it can support new roof top units or not. Often tenants remodel commercial spaces for their needs and also sometime new air make-up units, exhaust fans and HVAC units need to add.
What is Roof Top Unit: A packaged rooftop unit or RTU is a kind of HVAC system that has all the components needed to supply conditioned air in one brief unit. Packaged rooftop units are naturally found in light and large commercial applications. They are very famous in the construction industry with retail and industrial properties.
The Roof-top Unit or Roof Top Air Handling Unit supplies Heating, Ventilation, and Air Conditioning (HVAC) to the space below. Air duct Smoke Detectors or Duct Detectors can be inside the Roof Top Unit or in the air ducts below it.
In this article we are going to show evaluations of two commercial spaces for new rooftop units; where one space was adding a commercial kitchen and needed new exhaust fans and air make-up unit while the other needed new cooling units to reverse all the extra heat that was coming.
New roof top units can be large and heavy and generally affect the existing roof structure; sp at first the existing roof structure is examined to know the size, space and span of the joists, location of bearing walls and girders and location of previous roof top units. Generally a typical commercial roof structure is constructed with steel bar joists which are mainly tagged by the manufacturer like Vulcraft who keep records of joists’ type to use in the projects. Next all the accurate measurements of the top and bottom flanges, the web members and the length of the joist has taken; besides all this contractors have to observe other parameters to make sure all new and previous load can be transferred to the supporting structure in the right way.
After that the ability of from the manufacturer is determined and/or is modeled as per its section properties which help the contractors to calculate the load carrying capacity of the steel joist. As previous joists don’t have a lot of extra load carrying capacity so they can be strengthened by welding steel rods and plates to the flanges. But it is always best to locate a new unit away from previous units and near the previous bearing wall or girder which will limit the amount of new load on the previous joints. So basically it is mandatory to examine a previous structure to know its strength and capacity and qualifying it accordingly the new one as it creates a good understanding of structural design as well as a wealth of knowledge of building construction.
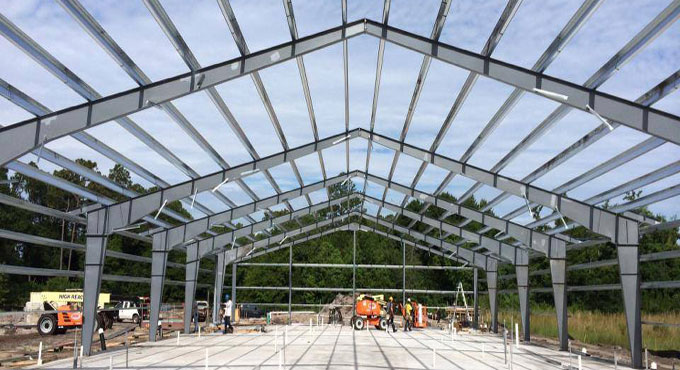
Read more
~~~~~~~~~~~~~~~~~~~~~~~~
Published By
Rajib Dey
www.constructioncost.co
~~~~~~~~~~~~~~~~~~~~~~~~