It takes huge time and labor to remove a subsisting concrete slab. In this regard, the most suitable process is to pour a new layer over the subsisting slab.
Thus, the requirement for labor will be reduced significantly as well as the money and resources will also be saved greatly. But, once the new layer is poured perfectly, it will only be as secure and durable similar to the older slab under it.
Increases the Level: The level will be increased by several inches while pouring a new layer of concrete over a subsisting walkway, patio or porch. If the slab puts up to a door, there may not be required clearance for the door to open with the lifted surface.
Towards a walkway, increasing the level by several inches can give out its alignment with the driveway, steps or another structure. When a slight ramp is added from the driveway to the increased surface, a trip hazard is reduced and the debris is retained from being collected in the corner.
Fewer Years of Service: A well-poured concrete slab containing a deep, strong foundation can survive for 30 to 40 years. Pouring concrete over old concrete rather than directly over a new gravel foundation restrains the scope to enhance the longevity of the slab.
The longevity of the new concrete is mainly dependent on the condition of the subsisting slab. If the foundation under the slab is not strong, the new concrete may sink or produce deep potholes.
Bonding: If new concrete is attached with the subsisting slab, cracks may occur. Retaining the new concrete from tying to the subsisting slab, new damage can’t develop as well as any damage in the old slab from extending to the new one. It makes both slabs adaptable to shrink and enlarge when temperatures change. To get rid of bonding, plastic/sand or other long-lasting material are arranged among the two layers of the slabs.
Maintenance: Due to its robust strength and low maintenance cost, the concrete is becoming popular. A slab poured over a subsisting slab may experience frost heave damage and cracks. The damages should be repaired immediately as soon as they form so that they can’t be expanded. The new layer must be sealed with deep penetrating sealer to get rid of water damage. If there are long, deep cracks, analyze the damage to find out any structural problem.
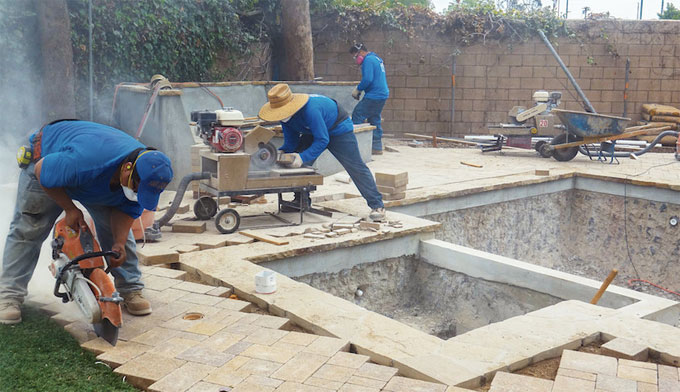
Read more
~~~~~~~~~~~~~~~~~~~~~~~~
Published By
Rajib Dey
www.constructioncost.co
~~~~~~~~~~~~~~~~~~~~~~~~
Thus, the requirement for labor will be reduced significantly as well as the money and resources will also be saved greatly. But, once the new layer is poured perfectly, it will only be as secure and durable similar to the older slab under it.
Increases the Level: The level will be increased by several inches while pouring a new layer of concrete over a subsisting walkway, patio or porch. If the slab puts up to a door, there may not be required clearance for the door to open with the lifted surface.
Towards a walkway, increasing the level by several inches can give out its alignment with the driveway, steps or another structure. When a slight ramp is added from the driveway to the increased surface, a trip hazard is reduced and the debris is retained from being collected in the corner.
Fewer Years of Service: A well-poured concrete slab containing a deep, strong foundation can survive for 30 to 40 years. Pouring concrete over old concrete rather than directly over a new gravel foundation restrains the scope to enhance the longevity of the slab.
The longevity of the new concrete is mainly dependent on the condition of the subsisting slab. If the foundation under the slab is not strong, the new concrete may sink or produce deep potholes.
Bonding: If new concrete is attached with the subsisting slab, cracks may occur. Retaining the new concrete from tying to the subsisting slab, new damage can’t develop as well as any damage in the old slab from extending to the new one. It makes both slabs adaptable to shrink and enlarge when temperatures change. To get rid of bonding, plastic/sand or other long-lasting material are arranged among the two layers of the slabs.
Maintenance: Due to its robust strength and low maintenance cost, the concrete is becoming popular. A slab poured over a subsisting slab may experience frost heave damage and cracks. The damages should be repaired immediately as soon as they form so that they can’t be expanded. The new layer must be sealed with deep penetrating sealer to get rid of water damage. If there are long, deep cracks, analyze the damage to find out any structural problem.
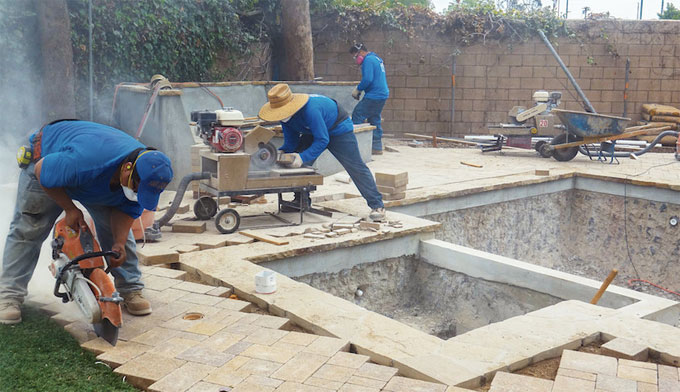
Read more
~~~~~~~~~~~~~~~~~~~~~~~~
Published By
Rajib Dey
www.constructioncost.co
~~~~~~~~~~~~~~~~~~~~~~~~