In this exclusive civil engineering article, you will know the difference between the main Bars and Distribution Bars in slab reinforcement.
Main bars and Distribution bars are vital terms which are found in slab reinforcements. In this civil engineering article, you will come to know the variations among main bar and distribution bar in slab as well as where these bars should be arranged in R.C.C slab.
MAIN BARS IN SLAB:
~~~~~~~~~~~~~~~~~~~~~~~~
Main bars and Distribution bars are vital terms which are found in slab reinforcements. In this civil engineering article, you will come to know the variations among main bar and distribution bar in slab as well as where these bars should be arranged in R.C.C slab.
MAIN BARS IN SLAB:
1. The main reinforcement should be arranged at the shorter extent of the slab, as in the shorter extent slab has to undergo High bending Moment that is called sagging or positive bending moment.
2. nbsp; Main reinforcement bars have to resist and bear all the tensile stresses, bending moment (Sagging), and superimposed load (Dead load) which are formed at the shorter extent of the slabs.
3. Main reinforcement bars are arranged in one way slab in one side (At shorter extent), but in two way slab, the bars are arranged in both ways.
4. In Flat plate slabs the main bars are arranged in one direction at bottom of the distribution bar (in shorter extent).
5. Main bars in the slabs should not be under 8 mm while applying (H.Y.S.D) or 10 mm for plain bars.
DISTRIBUTION BARS IN SLAB:
1. Distribution reinforcement bar should be arranged at the longest side extent of the slab.
2. Distribution bar are specifically created to allocate the super imposed load consistently or resist the Shrinkage stresses which are formed because of fluctuation of temperature in winter or summer.
3. In Flat plate slab the, the distribution bars are arranged in one direction at top of main bar (in longest extent).
4. The distribution bars should not be under 8 mm in a diameter or not in excess of 1/8 of the thickness of the R.C.C slabs.
5. The distribution bars are arranged to retain the mesh in exact location and keep the center to center c/c, bars spacing among main bars.
VARIATION AMONG BETWEEN MAIN BARS AND DISTRIBUTION BARS:
1. The Main bars are generally arranged at the bottom of distribution bar in slabs whereas distribution bars are arranged on the top of the main bar.
2. The Main bars are arranged in the shorter extent of the slabs whereas distribution bars are arranged in the longer extent of the slabs.
3. The main reinforcement is arranged to resist the bending moment, tensile stresses and superimposed load whereas distribution bars are utilized to allocate the load uniformly as well as withstand the shrinkage stress (Temperature discrepancy) or retain the mesh in exact location.
4. Main bars in the slab should not be under 8 mm when (HYSD) or 10 mm bars are used. But, when, plain bars and the distribution bars are used, it should not be under 8 mm diameter and the bar should not be in excess of 1/8 of the thickness of the slab.
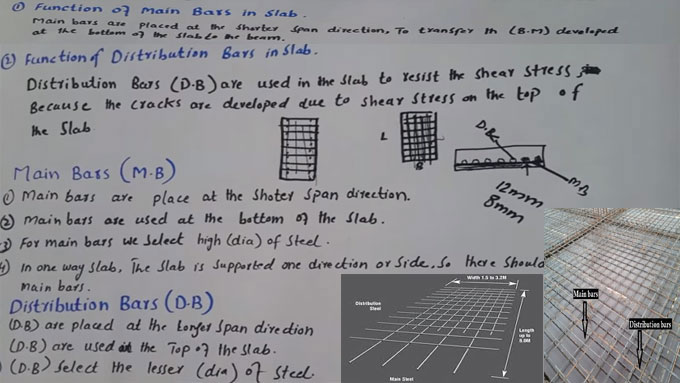