In order to create the design of foundations in a cost-effective manner as well as resolve practical construction issues, some factors should be taken into consideration.
Tips to create the design of the foundations in a cost-effective manner and avoid construction issues at job site.
~~~~~~~~~~~~~~~~~~~~~~~~~
Published By
Rajib Dey
www.constructioncost.co
~~~~~~~~~~~~~~~~~~~~~~~~~
Tips to create the design of the foundations in a cost-effective manner and avoid construction issues at job site.
a. Formation of the foundation should be shallow
b. Curtail construction cost of the foundation
c. Awareness of structural designer
d. Resist the application of costly and complicated formworks
e. Consistency of site investigation
f. Take decision to build up rapid or slow foundation
g. Impact of foundation construction on the ground and structures at area of the foundation
h. Disparities in foundation geometry and requisite of diverse joints
i. Effect of objectionable elements on constructed foundation
b. Curtail construction cost of the foundation
c. Awareness of structural designer
d. Resist the application of costly and complicated formworks
e. Consistency of site investigation
f. Take decision to build up rapid or slow foundation
g. Impact of foundation construction on the ground and structures at area of the foundation
h. Disparities in foundation geometry and requisite of diverse joints
i. Effect of objectionable elements on constructed foundation
Build up the Foundation as Shallow for saving
It is recommended to make the foundation shallow as much as possible. Make the best use of the size to sufficiently support loads and resist ecological impacts. Proper care should be taken to keep the depth and width of the foundation within limit.
This measure should be mostly suitable where the foundation is built up in completely saturated soil in which issues may arise because of existence of water. The cost is increased significantly with regards to the foundation developed in dry soil condition.
Decrease Cost of Foundation Construction: This can happen with a constant modification of construction methods and costs as the frugality of design differs significantly and usable standard might be obsolete.
To get more information, go through the following article theconstructor.org
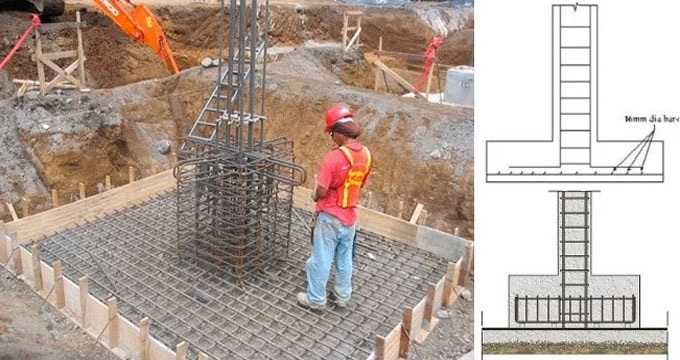
Published By
Rajib Dey
www.constructioncost.co
~~~~~~~~~~~~~~~~~~~~~~~~~