This civil engineering article sheds light on the required steps for post-concrete inspection as soon as decluttering of any concrete structure is completed.
The activities prior to arrange concrete comprise of utilization and maintenance of curing compound or other techniques of curing, form removal, concrete repair and preservation of concrete cubes. The subcontractor will inform QA/QC that curing is retained by the submittal of curing records.
Some vital Inspection points:
Given below, the details about major key inspection items to be examined and/or checked in the context of concrete post placement activities:
• Ensure that the necessary method of curing is prepared.
• Ensure that the placement is examined constantly to assure uninterrupted curing (watch for dry spots).
• Ensure that curing is retained for a prolonged time if necessary.
• Ensure that proper protection against bad weather is taken when necessary (hot or cold weather) as indicated in specifications.
• Ensure that concrete forms are departed in exact position for prolonged time to assure that form removal will keep concrete undamaged or workers (take precautions concerning the forms supporting the weight of the concrete to make sure the concrete has attained adequate strength to sustain its own weight)
• When repair of concrete is essential, check that it is repaired compliant with specifications (on the basis of the intensity of the repair, verify if a nonconformance report is necessary)
• Ensure that concrete cylinders are preserved on site in conformity with BS codes and job site requirements
• Ensure that concrete cylinders are transported to the testing laboratory and consequently tested compliant with BS and job site requirements Documentation
The Concrete Pour Card (Attached at the end) and Concrete Test Report as well as all supporting documents associated with the concrete pour should be arranged in the master file for the specific concrete pour. These files should be retained during the construction process and prepared in compliance with the methods of Control of Quality Records. There should be a proper labeling system for the project that sustains traceability among the concrete test report and the Concrete Pour Card.
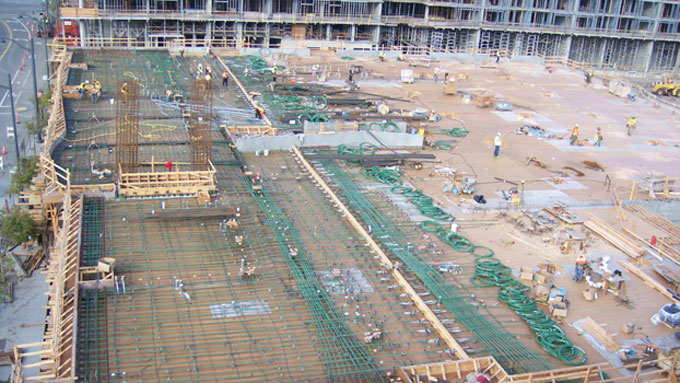
Read more
~~~~~~~~~~~~~~~~~~~~~~~~~
Published By
Rajib Dey
www.constructioncost.co
~~~~~~~~~~~~~~~~~~~~~~~~~
The activities prior to arrange concrete comprise of utilization and maintenance of curing compound or other techniques of curing, form removal, concrete repair and preservation of concrete cubes. The subcontractor will inform QA/QC that curing is retained by the submittal of curing records.
Some vital Inspection points:
Given below, the details about major key inspection items to be examined and/or checked in the context of concrete post placement activities:
• Ensure that the necessary method of curing is prepared.
• Ensure that the placement is examined constantly to assure uninterrupted curing (watch for dry spots).
• Ensure that curing is retained for a prolonged time if necessary.
• Ensure that proper protection against bad weather is taken when necessary (hot or cold weather) as indicated in specifications.
• Ensure that concrete forms are departed in exact position for prolonged time to assure that form removal will keep concrete undamaged or workers (take precautions concerning the forms supporting the weight of the concrete to make sure the concrete has attained adequate strength to sustain its own weight)
• When repair of concrete is essential, check that it is repaired compliant with specifications (on the basis of the intensity of the repair, verify if a nonconformance report is necessary)
• Ensure that concrete cylinders are preserved on site in conformity with BS codes and job site requirements
• Ensure that concrete cylinders are transported to the testing laboratory and consequently tested compliant with BS and job site requirements Documentation
The Concrete Pour Card (Attached at the end) and Concrete Test Report as well as all supporting documents associated with the concrete pour should be arranged in the master file for the specific concrete pour. These files should be retained during the construction process and prepared in compliance with the methods of Control of Quality Records. There should be a proper labeling system for the project that sustains traceability among the concrete test report and the Concrete Pour Card.
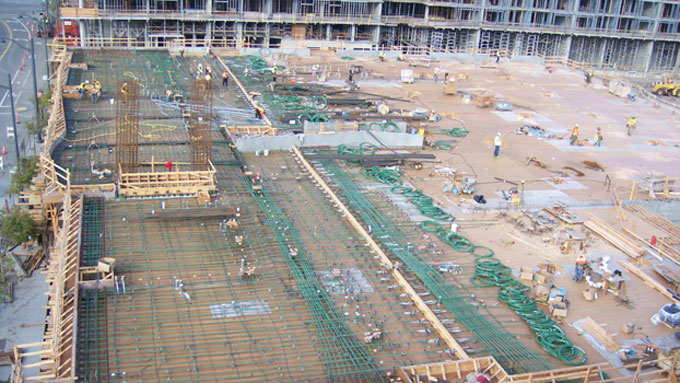
Read more
~~~~~~~~~~~~~~~~~~~~~~~~~
Published By
Rajib Dey
www.constructioncost.co
~~~~~~~~~~~~~~~~~~~~~~~~~