How estimation done: Costs are generally estimated with the help of some methods that are found in Time Management idea such as one-point estimating, analogous estimating, parametric estimating and three-point or PERT estimating; besides all of this there is a different kind of estimation named method of estimation.
~~~~~~~~~~~~~~~~~~~~~~~~
Bottom-up estimation is involved in the final distribution time of a project where it adds estimation of costs at each activity or work package, turning it up into control units and then finally works on whole project estimate. So the estimated created by following steps:
• Project management software: There is various kind of software that increases calculation speed needed to estimate costs and the calculations included direct, indirect, overhead and fixed cost calculations for many activities.
• Deciding resource cost rates: resources can be various kinds like human resources, vendors, consultants, suppliers, external technicians etc. and the project managers are aware about the involved rate for the resource cost.
• Reserve analysis: It gathers identification of activities with significant risks and resolution of all efforts needs to manage the occurred risks.
• Cost of quality: The quality efforts are divided as Cost of Quality.
• Deciding resource cost rates: resources can be various kinds like human resources, vendors, consultants, suppliers, external technicians etc. and the project managers are aware about the involved rate for the resource cost.
• Reserve analysis: It gathers identification of activities with significant risks and resolution of all efforts needs to manage the occurred risks.
• Cost of quality: The quality efforts are divided as Cost of Quality.
In the time working with integration, often it is asked about estimation of interfaces that follows below kind of scenarios:
• In the New implementation of Sap, the project manager has to execute lots of interfaces to join with the previous systems
• In the B2B integration, a lot of new pattern and messages will come
• Movement from one integration broker to another.
• In the B2B integration, a lot of new pattern and messages will come
• Movement from one integration broker to another.
When any of the scenarios will come interfaces are estimated by following the steps and the development is shown there:
1. Identification
2. System interactions with supported adapters
3. Specification
4. Development
5. Testing and fixing
6. Transport and configuration
7. Document
8. Going live
9. Support.
2. System interactions with supported adapters
3. Specification
4. Development
5. Testing and fixing
6. Transport and configuration
7. Document
8. Going live
9. Support.
All of the steps take extra time that will expand the initial time. The 80/20 principle was invented a long ago that states that spend less time to do more work and if more time spends in the beginning of the estimation then the whole process might take longer time to end. To avoid this scenario, it is important to study about the process and understands it properly then starts the work and as there are more variations of the interfaces that look similar then it will be easy to arrange them as per order.
It must keep in mind that performing estimation is not an easy task as there will be many unknown details about development that can be seem unclear before started; so just go through them and make a detailed report.
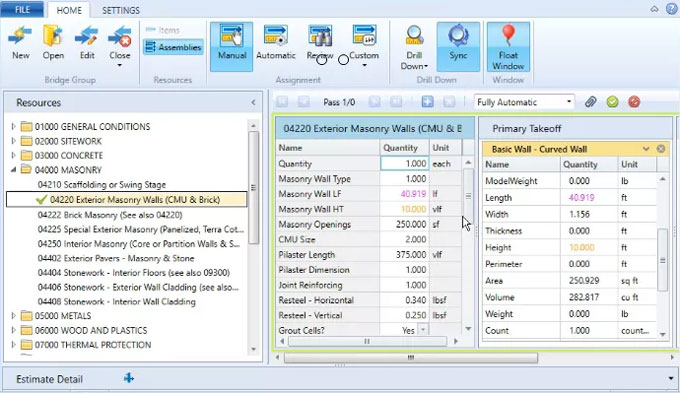
QTO is only one of many key aspects of best practice, consistent, and efficient construction cost estimating. Here's a list of IMPORTANT aspects that consider Owner, Builder, and AE requirements.
ReplyDelete1. EXPERIENCE, EXPERIENCE, EXPERIENCE. Nothing is more important than decades of actual experience in the field as well as detailed line item experience.
2. COMMUNICATION - Use industry standard terms in plain English for each construction task. Minimize the use of acronyms and/or abbreviations. In fact only use abbreviations for units of measure.
3. Common data format - Use CSI MasterFormt (50 division) to organize data.
4. Detail - Assure labor, material, and equipment breakdowns are available for EACH task as appropriate.
5. Integrated your work with a LOCALLY RESEARCHED unit price commercial construction cost data base. You don't know everything, and even if you did, this is a great way to supplement your data. DO NOT USE a national unit cost book and/or location factors/indexes. The latter will introduce significant error.
QTO is only one of many key aspects of best practice, consistent, and efficient construction cost estimating. Here's a list of IMPORTANT aspects that consider Owner, Builder, and AE requirements.
ReplyDelete1. EXPERIENCE, EXPERIENCE, EXPERIENCE. Nothing is more important than decades of actual experience in the field as well as detailed line item experience.
2. COMMUNICATION - Use industry standard terms in plain English for each construction task. Minimize the use of acronyms and/or abbreviations. In fact only use abbreviations for units of measure.
3. Common data format - Use CSI MasterFormt (50 division) to organize data.
4. Detail - Assure labor, material, and equipment breakdowns are available for EACH task as appropriate.
5. Integrated your work with a LOCALLY RESEARCHED unit price commercial construction cost data base. You don't know everything, and even if you did, this is a great way to supplement your data. DO NOT USE a national unit cost book and/or location factors/indexes. The latter will introduce significant error.